VAPOR RECOVERY SYSTEM FOR TERMINALS
A standard Cool Sorption Vapour Recovery Unit (VRU) is based on the Carbon Vacuum Adsoprtion (CVA) process. However, for some customers this technology is not advantageous because of size, special design conditions, lack of absorbent etc. For such situations, Cool Sorption also offers a range of simple variations to the CVA process as well as alternative, custom-made designs.
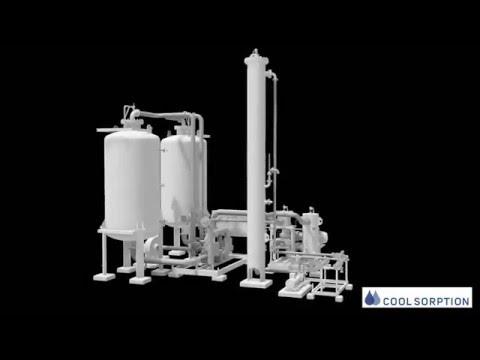
CVA (Carbon Vacuum Adsorption) – 2 activated carbon beds
The by far most commonly used VRU technology is based on adsorption on activated carbon followed by regeneration under vacuum. In Cool Sorption terminology we call it the CVA (Carbon Vacuum Adsoprtion) process. This process utilises two or more fixed beds filled with activated carbon (AC), a vacuum pump and an absorber column

- The inlet gasses to the VRU (typically containing 20-50 vol% hydrocarbons) are led to the AC beds. Due to the microporous structure and high surface area of activated carbon, the hydrocarbon gasses are adsorbed in a thin layer on the surface of the activated carbon, resulting in a very low concentration (10 g/Nm3 to 150 mg/Nm3) of hydrocarbons in the vapours exiting the AC beds. At any time, one of the beds is in “desorption” mode (i.e. regenerating by removing the adsorbed hydrocarbon gasses), while the other is in “adsorption” mode (i.e. receiving and adsorbing the incoming hydrocarbon gasses).
- Before the capacity of a carbon bed in adsorption mode is reached (i.e. before a breakthrough can occur), the bed shifts to regeneration mode. The operation of the beds is switched in this way every 15 minutes. When in regenerative mode, the hydrocarbon gasses are desorbed from the activated carbon using a vacuum pump.
- Regeneration of the AC beds takes place in three stages. In the first stage, the bed is evacuated of remaining inlet vapours left in the void spaces of the carbon bed vessel. In the second stage, the pressure in the bed continues to fall until it reaches a level at which the hydrocarbons begin to desorb from the surface of the activated carbon. The bulk of the hydrocarbons are removed during this stage. During the third stage, a small bleed of (ambient) purge air is introduced into the AC bed to assist the removal of the remainder of the hydrocarbons from the activated carbon and thus complete the regeneration process.
- The gas recovered with the vacuum pump will have a very high concentration of the VOC gasses (approx. 95 vol% VOC in 5 vol% air). This gas is led to an absorber column, where most of the hydrocarbons are absorbed in a counter-current flow of an appropriate absorbent.
- The gas exiting the absorber column will be saturated with hydrocarbon gasses from the absorbent and is recycled by mixing it with the inlet gasses to the VRU, going to the activated carbon beds.
As mentioned above, the AC beds are regenerated by means of vacuum; the vacuum pump system is therefore a vital component of the VRU. During the regeneration phase, the level of vacuum drawn in the AC beds is between 100 and 50 mbara.
Based on many years of experience with CVA systems, Cool Sorption launched a series of pre-engineered, standardised VRUs – especially for truck and railway terminals – in 2013. These VRUs (named Depot Series™ or DS-Series™) are mainly for terminals with low to medium throughput and have proven extremely reliable and successful.